Scaffolding mesh is an important safety feature on construction sites. It’s made from strong synthetic materials that are designed to protect both workers and the environment. This safety measure helps to block out wind, dust, and debris while still allowing fresh air to circulate in the work area.
Why Wind and Dust Protection is Important
Wind and dust protection is essential in modern construction. Without proper safeguards in place, construction sites can experience:
Choosing the right scaffolding mesh is a crucial decision in planning construction projects. It affects various aspects of site operations:
- Poor visibility, which can put workers at risk
- Unhealthy air quality
- The danger of objects falling from above
- Pollution of the surrounding environment
- Possible legal issues with local authorities
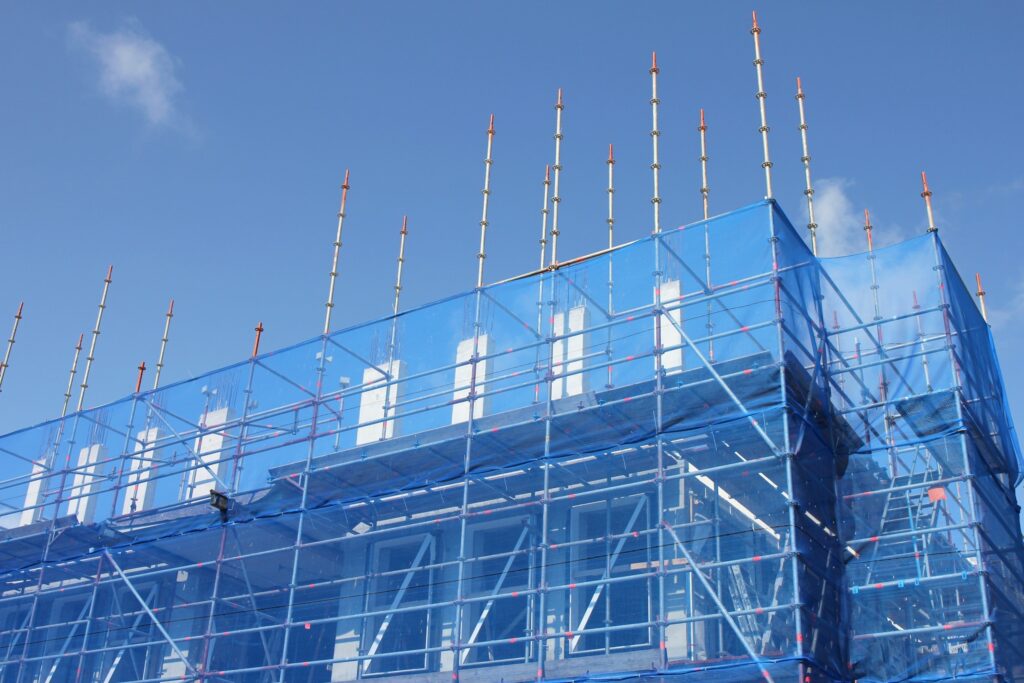
Choosing the Right Scaffolding Mesh
When it comes to selecting scaffolding mesh, there are several factors that need to be taken into account:
- Material Composition – how durable and weather-resistant the mesh is
- Protection Level – what percentage of coverage is required
- UV Resistance – how well the mesh can withstand sunlight exposure over time
- Visibility – any specific colour requirements for safety purposes
- Installation Requirements – how easy it is to set up and maintain the mesh
- Compliance Standards – whether or not the mesh meets local regulations
The choice of scaffolding mesh can have a direct impact on the success of a project, the safety of workers, and the protection of the environment. These barriers are crucial for ensuring that construction sites operate smoothly while also keeping people and nearby areas safe from potential dangers.
The Role of Scaffolding Mesh in Construction Safety
Scaffolding mesh serves as a critical safety barrier on construction sites, creating a protective shield against various hazards. This essential component transforms standard scaffolding structures into comprehensive safety systems.
Safety Enhancement on Construction Sites
- Prevents tools and materials from falling to lower levels
- Creates physical barriers between work zones
- Reduces risks of accidents from airborne debris
- Maintains clear sight lines while providing protection
Worker Protection Benefits
- Shields workers from harsh weather conditions
- Minimises exposure to harmful UV rays
- Reduces wind impact at elevated heights
- Creates stable working environments in varying conditions
Environmental Impact Control
- Contains construction dust within the work zone
- Prevents debris dispersion to surrounding areas
- Protects neighbouring properties from construction impacts
- Reduces noise pollution through sound absorption
The implementation of scaffolding mesh directly impacts site safety metrics through:
Accident Prevention
- Catches falling objects
- Prevents worker falls
- Maintains secure work boundaries
Health Protection
- Filters harmful particles
- Reduces exposure to construction dust
- Controls airborne contaminants
Site Management
- Defines clear work zones
- Improves site organisation
- Enhances visual safety markers
Proper scaffolding mesh installation creates controlled environments that protect both workers and the surrounding area. These protective barriers establish essential safety protocols while maintaining efficient construction operations.
Selecting appropriate scaffolding mesh requires careful consideration of material properties, protection requirements, and site-specific conditions. The right choice can significantly impact construction site safety, project efficiency, and environmental protection.
Find more on: Scaffold Mesh: An Overlooked Safety Essential on Busy Sites
Material Selection: Polyethylene vs Polypropylene in Scaffolding Mesh
Polyethylene Scaffolding Mesh
- High tensile strength-to-weight ratio
- Superior flexibility and impact resistance
- UV-stabilised options available
- Cost-effective solution for short-term projects
- Excellent weather resistance properties
Polypropylene Scaffolding Mesh
- Enhanced durability under extreme conditions
- Higher melting point (160°C compared to polyethylene’s 120°C)
- Chemical resistance against common construction materials
- Ideal for long-term construction projects
- Superior tear resistance
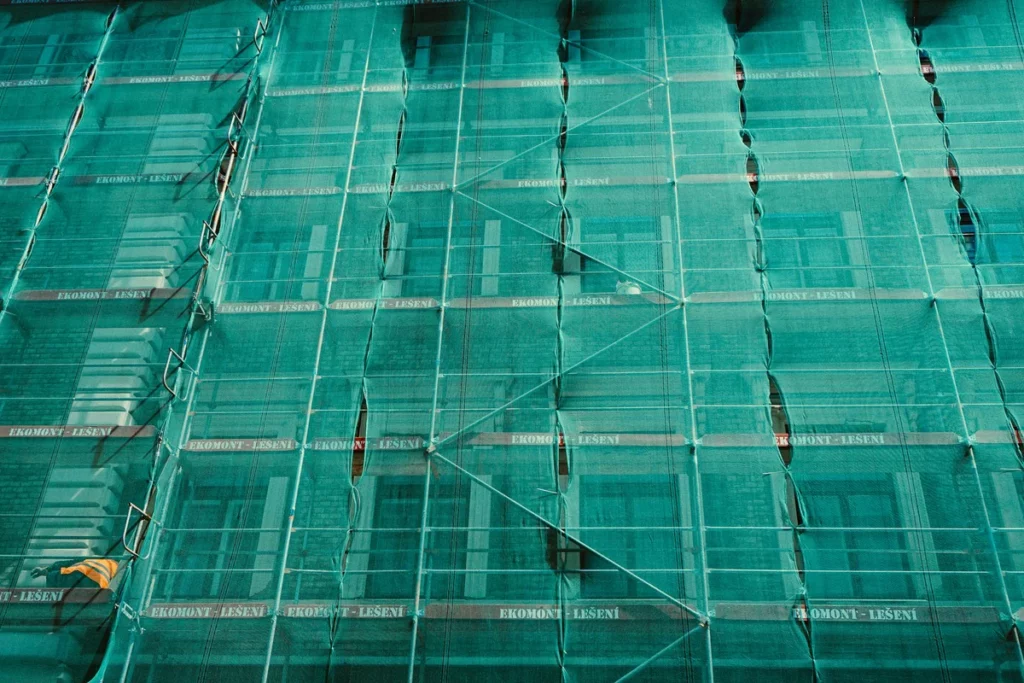
The material choice between polyethylene and polypropylene depends on specific project requirements:
Temperature Considerations
- Polyethylene performs well in moderate temperatures
- Polypropylene maintains stability in high-temperature environments
- Both materials require UV stabilisation for prolonged sun exposure
Strength Requirements
Polyethylene offers:
- 15-20% lighter weight
- Greater flexibility
- Easier installation
Polypropylene provides:
- Higher tensile strength
- Better abrasion resistance
- Enhanced load-bearing capacity
Cost Analysis
- Initial Investment
- Polyethylene: Lower upfront costs
- Polypropylene: Higher initial investment
- Long-term Value
- Polyethylene: Suitable for projects under 12 months
- Polypropylene: Cost-effective for extended use
Environmental Factors
- Wind Resistance
- Polyethylene: Suitable for low to moderate wind conditions
- Polypropylene: Preferred for high-wind environments
- Dust Control
- Both materials offer effective dust containment
- Mesh density determines filtration efficiency
- Available in various permeability ratings
The selection process should account for:
- Project duration
- Local weather conditions
- Site-specific requirements
- Budget constraints
- Environmental considerations
These material characteristics form the foundation for effective scaffolding mesh selection, ensuring optimal protection against wind and dust while maintaining site safety standards.
Exploring Different Types of Scaffolding Mesh for Specific Construction Needs
Construction sites present diverse challenges that require specific types of protective netting. Each variant of scaffolding mesh serves distinct purposes and offers unique advantages for particular construction scenarios.
1. Standard Netting
- Basic debris containment
- Cost-effective solution for general construction work
- Suitable for low-risk environments
- Available in various densities (50% to 90% coverage)
2. Fire Retardant Netting
- Engineered with flame-resistant properties
- Essential for welding areas and high-heat zones
- Meets strict safety standards for fire prevention
- Self-extinguishing capabilities
- Ideal for industrial construction sites
3. Windbreak Netting
- Designed for high-rise construction projects
- Enhanced wind resistance capabilities
- Reduces wind speed by up to 75%
- Prevents material displacement
- Enables work continuation during windy conditions
The selection between these types depends on specific site requirements:
- Height of construction – Taller buildings require stronger windbreak options
- Location exposure – Coastal areas need more robust wind protection
- Project duration – Long-term projects benefit from more durable materials
- Site activities – Welding operations necessitate fire-retardant options
- Local weather conditions – Areas with high winds require specialised windbreak solutions
Each type undergoes rigorous testing to ensure compliance with Australian construction standards and safety regulations, such as those outlined in this OSHA publication. The choice of appropriate netting directly impacts worker safety, project efficiency, and environmental protection measures.
Essential Features to Look For When Selecting Scaffolding Mesh
UV Resistance
UV resistance stands as a critical feature in scaffolding mesh selection. Construction sites face constant exposure to harsh sunlight, making UV-resistant mesh essential for:
- Preventing material degradation
- Maintaining structural integrity
- Extending service life
- Reducing replacement frequency
High Visibility Colours
High visibility colours serve multiple safety functions in scaffolding mesh:
Safety Enhancement
- Bright colours alert workers to mesh boundaries
- Improved visibility during low-light conditions
- Clear demarcation of work zones
- Enhanced site safety management
Colour-Coding Benefits
- Different zones marked by distinct colours
- Quick identification of restricted areas
- Efficient site navigation
- Emergency response facilitation
Interestingly, it’s worth noting that some colors of plastic can be weaker or stronger than others, which could influence the choice of high visibility colors used in scaffolding mesh.
Tensile Strength Requirements
The mesh’s tensile strength requires careful consideration, with recommended specifications:
Minimum breaking strength: 2.0kN Elongation at break: 15-20% UV resistance rating: 90%+ after 2000 hours exposure
Additional Essential Features
Additional essential features include:
- Fire-retardant properties
- Weather resistance capabilities
- Anti-static characteristics
- Reinforced edges for durability
- Proper mesh size for dust control
- Strong fixing points
- Tear resistance properties
These features combine to create a robust protective barrier that maintains its effectiveness throughout the project’s duration while meeting safety standards.
Evaluating Protection Levels: Ensuring Effective Dust Containment and Debris Minimisation with Scaffolding Mesh
Effective dust containment requires strategic assessment of mesh density and permeability ratings. A mesh with 90% containment efficiency proves ideal for controlling fine dust particles, while maintaining adequate airflow for worker comfort and safety.
Key assessment criteria for dust containment include:
- Mesh aperture size – smaller openings (1-3mm) trap more dust particles
- Air permeability rating – optimal range between 15-25% for dust control
- Material density – higher density correlates with better containment
- Wind load resistance – prevents billowing and maintains dust barrier
Debris minimisation demands specific mesh characteristics:
- Heavy-duty reinforced edges to prevent tearing
- Double-stitched seams for enhanced strength
- Impact-resistant materials to catch falling objects
- Secure fixing points at 500mm intervals
Testing protocols help verify protection levels:
- Visual inspection – check for gaps or damage
- Smoke testing – reveals air leakage points
- Pressure differential monitoring – confirms proper containment
- Regular dust monitoring – measures effectiveness
Site-specific factors affecting containment levels:
Height of structure Prevailing wind conditions Types of construction activities Proximity to sensitive areas
Regular assessment of these protection measures ensures maintained effectiveness throughout the project lifecycle. For instance, understanding the bioavailability of certain materials used in scaffolding can significantly enhance dust control strategies. Furthermore, recent studies have shown that specific mesh characteristics can lead to improved performance in various environmental conditions. It’s also crucial to consider the impact of structural height on the overall efficacy of the dust containment measures implemented.
Navigating Safety Compliance: How Choosing the Right Scaffolding Mesh Helps Meet Construction Site Regulations
Construction site safety regulations demand strict adherence to specific standards for scaffolding mesh installation. The Work Health and Safety (WHS) regulations outline essential requirements for protective barriers on construction sites.
Key compliance requirements include:
- Minimum tensile strength specifications
- Proper mesh aperture size for dust containment
- Fire-resistance ratings for specific construction environments
- UV protection standards for extended outdoor exposure
- Height-specific requirements for different building levels
The selection of appropriate scaffolding mesh directly impacts regulatory compliance. Type-tested and certified mesh provides documented evidence of meeting safety standards, simplifying site inspections and regulatory approvals.
Critical safety standards to consider:
- AS/NZS 4576 – Guidelines for scaffolding
- AS 1576 – Scaffolding general requirements
- AS/NZS 4389 – Safety mesh specifications
Proper documentation and certification of scaffolding mesh materials serve as crucial evidence during safety audits. Regular inspection protocols must be established to maintain compliance throughout the project duration.
The integration of high-visibility elements and appropriate signage on scaffolding mesh supports workplace safety requirements. Reflective strips and warning markers enhance visibility during low-light conditions, meeting additional safety regulations for night work and emergency situations.
Selecting mesh with appropriate fire-retardant properties ensures compliance with fire safety regulations, particularly in high-risk construction environments or when working near potential ignition sources.
Installation & Maintenance Best Practices: Ensuring Optimal Performance from Your Chosen Scaffolding Mesh
Proper installation and maintenance protocols play a vital role in maximising scaffolding mesh effectiveness. The implementation of correct techniques ensures optimal wind and dust protection while maintaining site safety standards.
Essential Installation Steps:
- Secure mesh at regular intervals using appropriate fixings
- Install with consistent tension to prevent sagging
- Overlap sections by minimum 100mm
- Double-check all attachment points
- Position seams away from prevailing wind direction
Regular Maintenance Requirements:
- Daily visual inspections for tears or damage
- Weekly tension checks
- Monthly thorough examination of fixing points
- Immediate repairs or replacement of damaged sections
- Documentation of all maintenance activities
Worker Training Elements:
- Correct installation procedures
- Proper use of fixing tools and equipment
- Recognition of wear and damage signs
- Emergency response protocols
- Safe working practices at height
The establishment of a comprehensive maintenance schedule helps identify potential issues before they become critical. Regular cleaning of the mesh surface prevents dust build-up, which can affect its performance and longevity. Implementation of a robust reporting system enables quick identification and resolution of any mesh-related issues.
Proper storage practices between uses protect the mesh material from UV damage and extend its service life. Keeping detailed maintenance records aids compliance requirements and helps track the mesh’s performance over time.
Considering Environmental Impact: How Certain Types Of Scaffolding Mesh Contribute To Sustainability Efforts On Construction Sites
Sustainable construction practices demand environmentally responsible material choices. Modern scaffolding mesh options present significant opportunities for reducing environmental impact through:
1. Recyclable Materials
- High-density polyethylene (HDPE) mesh offers 100% recyclability
- Polypropylene variants can be repurposed into new construction materials
- Recycled content meshes reduce raw material consumption
2. Waste Reduction Features
- UV-stabilised meshes extend product lifespan
- Tear-resistant designs minimise replacement frequency
- Reusable configurations reduce disposal rates
3. Environmental Benefits
- Dust containment prevents air pollution
- Proper debris control protects local ecosystems
- Reduced material transport needs lower carbon emissions
4. Sustainable Manufacturing
- Low-energy production processes
- Minimal water consumption in manufacturing
- Reduced chemical usage compared to traditional materials
5. End-of-Life Management
- Dedicated recycling programmes
- Material recovery initiatives
- Waste-to-energy conversion options
The adoption of eco-friendly scaffolding mesh supports green building certifications and demonstrates environmental stewardship. Construction sites implementing recyclable mesh systems report up to 30% reduction in material waste, while maintaining essential safety and protection standards.
Conclusion
- Safety and Protection: High-quality mesh creates secure working environments through effective dust containment and wind protection
- Material Performance: Understanding polyethylene versus polypropylene characteristics ensures optimal durability and functionality
- Regulatory Compliance: Proper mesh selection helps meet construction safety standards and local building regulations
- Environmental Responsibility: Recyclable materials and waste reduction capabilities contribute to sustainable construction practices
The selection process requires careful consideration of specific project requirements, site conditions, and environmental factors. A systematic approach to evaluating mesh options—focusing on material properties, protection levels, and sustainability features—leads to enhanced site safety, improved worker comfort, and reduced environmental impact. This investment in appropriate scaffolding mesh delivers long-term benefits through increased project efficiency, regulatory compliance, and environmental stewardship.